N. D.
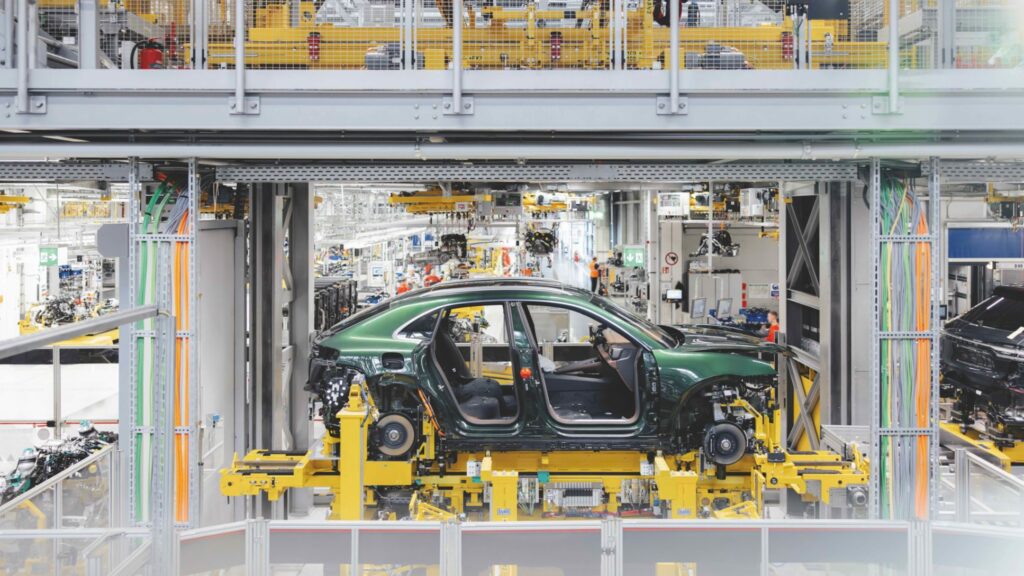
Vjenčanje je u toku, ali se ne svira valcer. Umjesto toga, tu su zvuci šuštanja, zujanja i udaranja – pozadinska muzika za modernu proizvodnju automobila u Porsche fabrici Leipzig. Karoserija Porsche Macana ofarbana u hrast zelenu metalik polako se spušta. Njegov vjerenik, šasija sa potpuno električnim pogonom, upravo je dovedena pomoću transportnog sistema bez vozača. Kao u usporenom snimku, dvije komponente se potpuno automatski spajaju i zašrafljuju prije nego što se unutrašnjost instalira. To je ono što se zove brak. Gdje god se proizvode vozila, ovo je centralni dio proizvodnje.
Za sada je dobro. Ali brak u Porsche fabrici u Leipzigu je poseban. Neobično složen, višestruk i efikasan. Na jednoj proizvodnoj liniji proizvode se tri različita koncepta pogona: benzinska, hibridna i električna vozila. Svaki dan se na ovaj način proizvodi oko 600 automobila Macan i Panamera vrhunskog kvaliteta za kupce širom svijeta.
Voditelj ceremonije za ove brakove je Sebastian Böttcher. Sertifikovani inženjer je planer opreme i razvio je sistem zajedno sa desetak svojih Porsche kolega. Bottcher, 40, rođen u Dresdenu, nosi odgovarajuću analogiju za svoj rad na svom zglobu: otmjeni sat kojim se počastio za svoj 30. rođendan. „Pogledajte“, kaže, pokazujući na zadnju stranu kućišta sata napravljenu od specijalnog stakla, iza koje se vidi nježni opružni mehanizam.
– Naša fabrika je kao sat, samo u drugoj skali, poručuje.
Temelji za potpuno remont ovog satnog mehanizma postavljeni su 2018. godine kada je Izvršni odbor odlučio da proizvede potpuno električni Macan. Odlučeno je da se model kreira u Lajpcigu, na postojećoj proizvodnoj liniji koja je do tada bila rezervisana za vozila sa motorom sa unutrašnjim sagorijevanjem ili hibridnim pogonom. Realizacija potpuno nove linije ne bi bila moguća na osnovu postojećih parametara.
– Ubrzo smo shvatili da ćemo morati u potpunosti da revidiramo postojeći brak i mnoge druge tokove rada u fabrici. Dodatni tip pogonskog sklopa je kao mali svijet za sebe, s novim zahtjevima, posebnim procedurama i posebnim alatima. Imali smo mnogo toga da naučimo, kaže Böttcher.
Jedan posebno složen problem: dok spoj između benzinskog ili hibridnog vozila uključuje spajanje podvozja i šasije na 20 mjesta, u potpuno električnom modelu postoji 50. Iako se ova promjena u početku može činiti nespektakularnom, uključivala je veliki izazov rukovanja ovim dodatnim radnim koracima na jednoj te istoj montažnoj liniji.
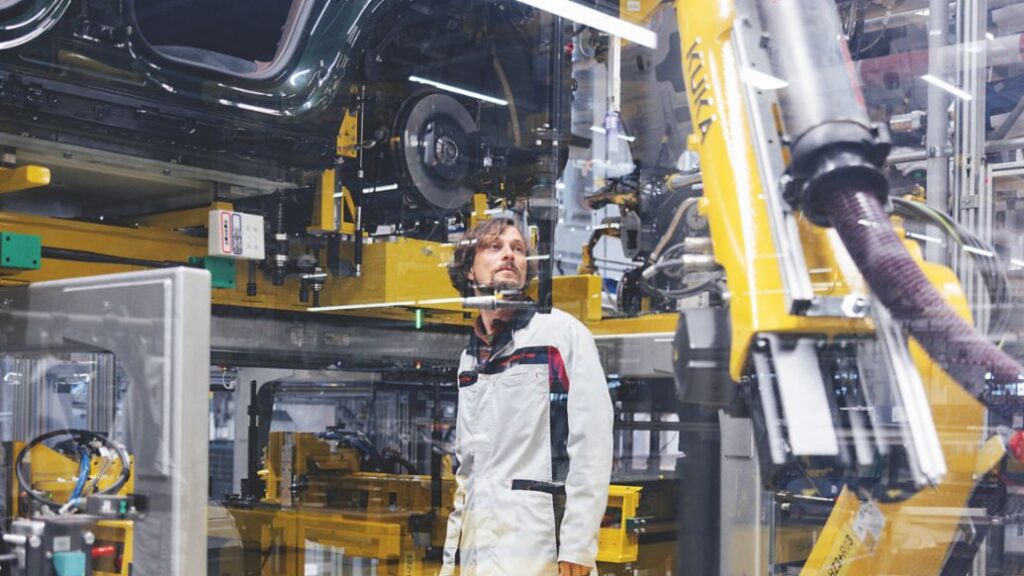
Da bi riješili ovaj problem, Sebastian Böttcher i njegov tim morali su ponovo izmisliti brak. Ono što su ranije bile četiri montažne stanice koje su se protezale na 24 metra, postalo je devet stanica na 60 metara. Ugrađeno je šest dodatnih robota i 18 automatskih vijčanih stanica.
I drugdje, Porsche je namjerno došao do novih ideja uz pomoć vanjskih partnera. Na primjer, razvio je automatski sistem za punjenje vijaka koji, ovisno o liniji proizvoda i fitingima, može podnijeti bilo koju veličinu i oblik zavrtnja, obrtni moment i ugao, pri nevjerovatno velikim brzinama. Razvijen je i mjerni uređaj koji trenutno ima patent na čekanju. Ovo redovno prolazi duž montažne linije kako bi se provjerila vretena vijaka tokom tekućih proizvodnih operacija. Kao rezultat toga, praktično nema vremena mirovanja ili kašnjenja.
Instaliran je i poseban sistem kamera koji autonomno ispituje površinu visokonaponskih baterija električnih vozila na strane predmete kao što su zabačene podloške ili matice.
– Sve u svemu, stvorili smo visoko produktivan sistem koji je neprimjetno ugrađen u sve tokove rada u postrojenju. Očigledno je da uvijek postoje stvari koje treba optimizirati, ali to je standardna procedura za nas u Porscheu, kaže Böttcher.
Važnost sagledavanja cjelokupne slike prilikom preispitivanja braka postaje očigledna kada razgovarate sa kolegama Sebastiana Böttchera u drugim odjelima.
– Princip biserne ogrlice ima ključnu ulogu u svemu što radimo ovdje, kaže Denny Schubert iz odjeljenja za sisteme upravljanja vozilima.
U Porscheu, ovo je koncept koji osigurava efikasno korištenje zaposlenika, minimizira skladištenje i savršeno sortira dijelove i šalje ih na montažnu traku u pravo vrijeme.
– Nastojimo da precizno upravljamo redoslijedom kojim se vozila obrađuju, poređana kao na nizu bisera, naglašava Schubert.
Porsche Plant Leipzig općenito planira 10 dana unaprijed. Ovo omogućava dobavljačima da precizno usklade svoju proizvodnju sa potrebama montažne trake i isporuče sve dijelove u tačno pravo vrijeme. Ovo je fundamentalno kada je u pitanju nesmetana proizvodnja jer su sva vozila koja se ovdje proizvode različita. Postoji teoretski bezbroj potencijalnih kombinacija modela, pogonskih tehnologija, livreja i detalja opreme.
– Proizvodnja tri različita tipa pogona na jednoj liniji je zahtjevna za sve u fabrici. Naš posao je veoma složen, dodaje Martin Reinbacher iz industrijskog inženjerstva.
Na primjer, morali su se naučiti dodatni koncepti sklapanja potpuno električnog Macana, a ergonomija brojnih radnih stanica je morala biti prilagođena.
– Sve je međusobno povezano. Moramo planirati na veoma umrežen i međuodjel da bismo došli do efikasnih rješenja. Ali vidimo da se ovo isplati svaki dan, objašnjava Reinbacher.
Princip biserne ogrlice je poput kompasa, osiguravajući da svaki korak proizvodnog procesa bude usklađen sa sljedećim. Rezultat je visoko precizna proizvodnja koja teče što je moguće glatko unatoč složenijim radnim procesima.